1. What is the melting point of plastic?
The melting point of plastic is the temperature at which it transitions from a solid state to a liquid state. The melting point of plastic depends on various factors, including the type of plastic, its chemical composition, and molecular structure.
There are many different types of plastics, each with a different melting point. Some plastics have low melting points, such as thermoplastic plastics like polyethylene (PE) and polypropylene (PP), which melt between 110 to 175 degrees Celsius. On the other hand, other plastics, like thermosetting plastics such as epoxy and polyester, have higher melting points, ranging from 150 to 300 degrees Celsius.
The melting point of plastic can also be influenced by the chemical components of the plastic. For example, PE has a lower melting point compared to PP because PE has more branching in its molecular structure. The molecular structure of plastic can also impact the melting point. For instance, PE has a more linear molecular structure compared to PP, resulting in a lower melting point.
The melting point of plastic is a critical parameter to know in plastic manufacturing. It determines the temperature required to melt the plastic to form various plastic products.
2. What's the melting point of plastic?
The melting temperature of plastic is a crucial parameter to be aware of in plastic manufacturing. It specifies the temperature required to melt the plastic in order to form various plastic products. Below are the melting temperatures of common types of plastic:
Materials | Melting Point Range (℃) |
ABS – acrylonitrile-butadiene-styrene | 190-270 |
ABS/PC Alloy | 245-265 |
Acetal | 180-210 |
Acrylic | 220-250 |
CAB – Cellulose Acetate Butyrate | 170-240 |
HDPE – High-Density Polyethylene | 210-270 |
LDPE – Low-Density Polyethylene | 180-240 |
Nylon 6 or Polyamide | 230-290 |
Nylon 6 (30% GF) | 250-290 |
Nylon 6/6 | 270-300 |
Nylon 6/6 (33% GF) | 280-300 |
Nylon 11 | 220-250 |
Nylon 12 | 190-200 |
PEEK – Polyether ether ketone | 350-390 |
Polycarbonate | 280-320 |
Polyester PBT | 240-275 |
PET (Amorphous) | 260-280 |
PET (semi-crystalline) | 260-280 |
Polypropylene (Homopolymer) | 200-280 |
Polypropylene (copolymer) | 200-280 |
Polypropylene (30% tank filled) | 240-290 |
Polypropylene (30% GF) | 250-290 |
Polystyrene | 170-280 |
Polystyrene (30% GF) | 250-290 |
PVC – Polyvinyl chloride | 160-210 |
SAN – Styrene acrylonitrile | 200-260 |
SAN (30% GF) | 250-270 |
TPE – Thermoplastic Elastomer | 260-320 |
3. How does the melting point of plastic affect its applications?
Plastic is a synthetic material with a wide range of applications in our daily lives. The melting point of plastic is one of its most important properties, influencing its usability in various applications.
3.1. Automotive and aerospace Industries
In packaging applications, the melting point of plastic affects its suitability for containing food and beverages. Plastics with lower melting points are often used to package products that need to be stored at low temperatures, such as frozen foods. This is because plastics with low melting points can withstand cold temperatures without cracking or breaking.
Plastics with higher melting points are typically used for packaging products that require high-temperature storage, such as hot beverages.
3.2. Automotive and aerospace Industries
In the automotive and aerospace industries, plastic is used to manufacture parts and components that require high durability and heat resistance. Plastics with high melting points are used to produce load-bearing components, such as car bodies and aircraft fuselages. This is because plastics with high melting points can withstand significant mechanical stress without deforming or becoming damaged.
Plastics with extremely high melting points, such as polyetherimide (PEI), are often employed in applications demanding exceptional heat resistance, such as rocket engine components.
3.3. Electronic Devices
In electronic devices, plastic is used to manufacture casings, components, and circuit boards. Plastics with low melting points are often used to produce casings and components that can be recycled. This is because plastics with low melting points can be more easily recycled compared to those with higher melting points.
Plastics with high melting points are typically employed in the production of circuit boards and components that require durability and high heat resistance.
3.4. Medical Equipment
In medical equipment, plastic is used to manufacture tubing, surgical instruments, and various other devices. Plastics with low melting points are often used to produce reusable medical equipment.
Plastics with high melting points are commonly used to manufacture medical devices that require durability and high heat resistance. This is because plastics with high melting points can withstand sterile conditions and sterilization processes without getting damaged.
3.5. Consumer Goods
In consumer goods, plastic is used to manufacture household items, toys, and various other products. Plastics with low melting points are often used to produce affordable household items. Plastics with high melting points are typically employed in the production of premium household items, such as high-quality plastic kitchenware.
4. What factors influence the melting temperature of plastic?
The melting temperature of plastic depends on several key factors, including:
The chemical structure of the polymer: Different types of plastics with different chemical structures will have different melting temperatures. For instance, plastics containing a higher number of hydrocarbon groups tend to have higher melting temperatures compared to plastics with different functional groups.
The degree of crystallinity: Crystalline plastics have higher melting temperatures compared to amorphous plastics. This is because the molecules in crystalline plastics are arranged in a specific order, making them more resistant to breaking apart.
The mass ratio of components in the plastic: The melting temperature of plastic can also be influenced by the mass ratio of its components. For example, ABS plastic is a thermoplastic composed of three types of monomers: acrylonitrile, butadiene, and styrene. The mass ratio of these monomers affects the melting temperature of ABS plastic.
Additives: Additives introduced into the plastic can impact its melting temperature. For example, heat stabilizers can be added to raise the melting temperature of the plastic.
5. Frequently asked questions
How can the melting point of plastic be determined?
There are several different methods to determine the melting point of plastic. A common method involves using a mercury thermometer. This method entails heating the plastic in a small glass container and recording the temperature at the moment the plastic begins to melt.
Can the melting point of plastic be altered?
Yes, the melting point of plastic can be altered by adding various additives. For example, fillers often reduce the melting point of plastic.
Is the melting point of plastic related to its strength?
The melting point of plastic is not directly related to its strength. However, plastics with higher melting points tend to have better strength than those with lower melting points. This is because plastics with higher melting points typically have a more tightly bonded molecular structure, making them more resistant to deformation or destruction.
Is the melting point of plastic related to its recyclability?
The melting point of plastic is related to its recyclability. Plastics with higher melting points are often easier to recycle than those with lower melting points. This is because plastics with higher melting points can be heated to higher temperatures without undergoing degradation, making them easier to melt and recycle.
Is there a way to improve the recyclability of low-melting-point plastics?
There are several ways to improve the recyclability of low-melting-point plastics. One way is to use additives that can increase the melting point of the plastic. For example, additives like fillers and reinforcing agents can help raise the melting point of the plastic.
Another way to improve the recyclability of low-melting-point plastics is to utilize advanced recycling methods. For instance, pyrolysis, a thermal decomposition process, can be used to recycle low-melting-point plastics into raw materials that can be used to produce new plastic.
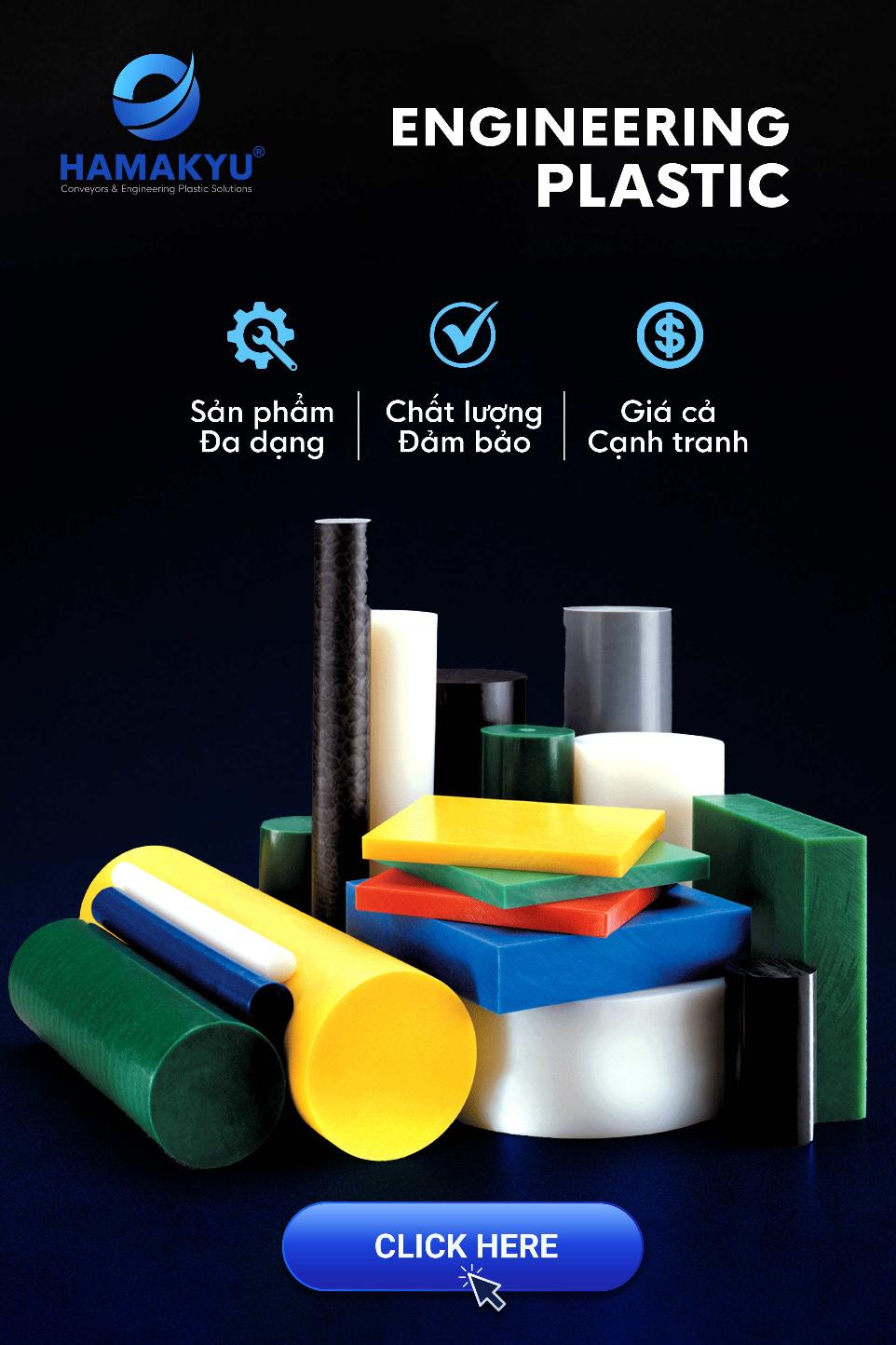