I. What is a non-stick additive?
Anti-stick additive, also known as anti-block additive, is a type of additive used in the production of plastic materials. Its main function is to prevent adhesion of the surface of plastic film or plastic sheet, which may occur during production, storage or transportation and use.
Anti-stick additive for plastic (antiblock masterbatch)
II. The role of anti-stick additives in the plastic industry
1. Prevent adhesion
Anti-blocking additives are used to prevent adhesion of plastic films or sheets to each other, especially during storage and transportation. These additives create a micro-rough surface on the plastic film, which reduces the blocking effect and allows for easy film separation. This is especially important in industries that use large amounts of plastic film, such as in packaging and agriculture.
Agricultural mulch film
2. Improve surface quality
In addition, anti-blocking additives also improve the transparency and transparency of plastic films, as well as reduce the coefficient of friction, making the films easier to handle and process. This is especially important in applications where the appearance and quality of the plastic film is critical, such as in food and consumer goods packaging.
Transparent wrapping film
3. Improve processing performance
On the processing side, anti-blocking additives also help reduce the force required to unwind or separate the plastic film, thereby improving efficiency and productivity in the manufacturing process. This is especially important in high-speed packaging lines where smooth and efficient plastic film handling is essential.
III. Types of anti-stick additives
1. Inorganic non-stick additive
The most common type of anti-blocking additive is inorganic particles, such as silica or talc. These particles are added to plastic during the manufacturing process, where they form a microscopic layer on the surface of the plastic, preventing it from sticking to other surfaces. Inorganic anti-blocking additives are highly effective and suitable for many plastic applications.
Gel silica
2. Organic non-stick additives
Another type of anti-blocking additive is organic particles, such as polyethylene wax or polypropylene wax. These particles work in a similar way to inorganic additives, forming a thin layer on the plastic surface to prevent adhesion. Organic anti-block additives are often preferred for applications where clarity and transparency are important because they have minimal impact on the appearance of the plastic.
Polyethylene wax
3. Specialized additives
In addition to inorganic and organic particles, there are specialized non-stick additives for specific applications. For example, for food packaging, anti-blocking additives that comply with food contact regulations are used to ensure the safety of packaged foods.
IV. Application of anti-stick additives in production
1. Extrusion
In extrusion, anti-blocking additives play an important role in preventing adhesion of film layers during production. This helps maintain the quality and appearance of the film as well as facilitates the handling and packaging of the final product. By reducing the coefficient of friction between film layers, anti-blocking additives also contribute to improving the overall efficiency of the extrusion process.
2. Injection molding
In injection molding, anti-blocking additives are used to prevent adhesion of plastic parts to the mold surface. This not only improves mold release characteristics but also enhances the surface finish of molded parts. Additionally, the use of anti-blocking additives in injection molding reduces wear on the mold, resulting in longer mold life and lower maintenance costs.
3. Blow molding
Similarly, in the blow molding process, anti-blocking additives are used to prevent adhesion of the plastic material to the mold surface. This results in smoother and more uniform wall thicknesses in blow molded products as well as improved mold release characteristics. The use of anti-blocking additives in blow molding also helps reduce the occurrence of defects such as blemishes and surface roughness, leading to higher final product quality.
Sources: cpiplastic.com
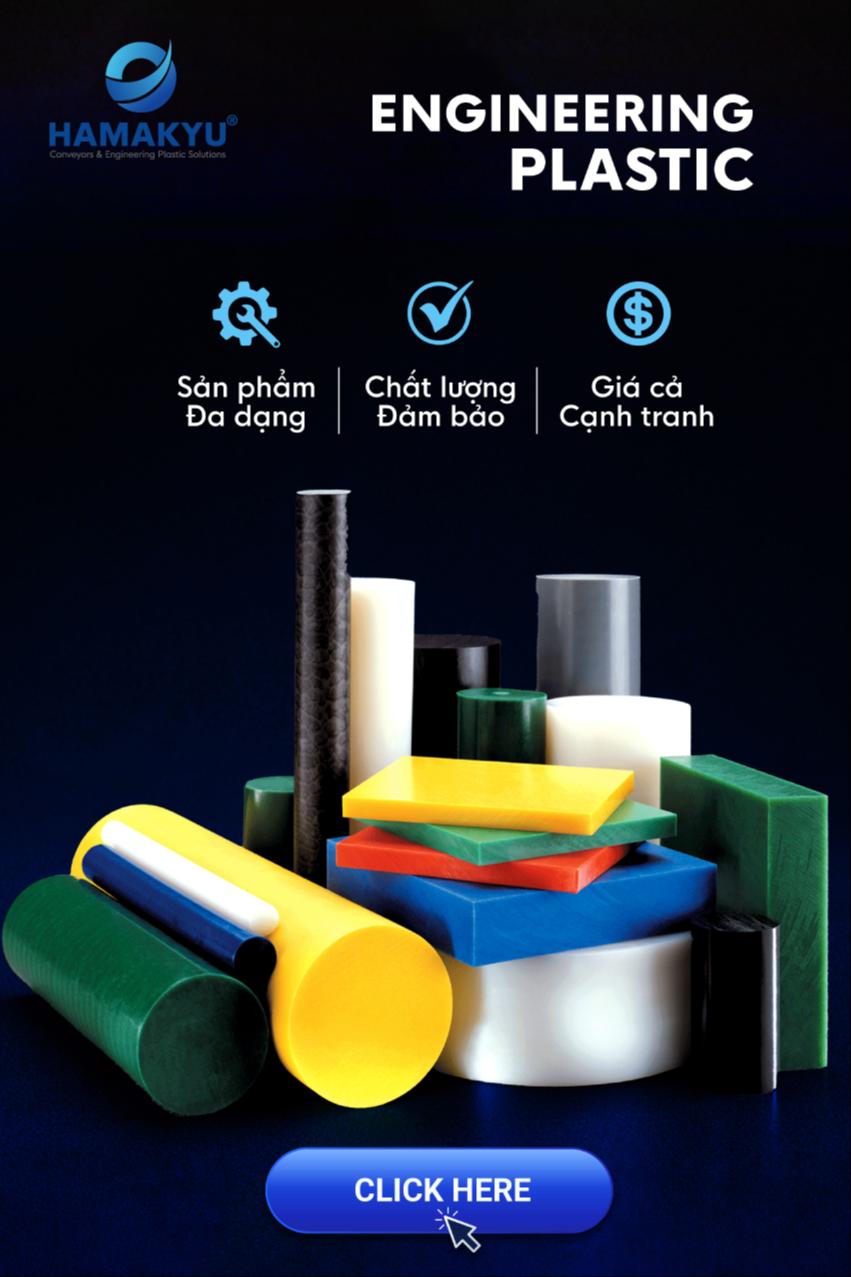