History
PC (Polycarbonate) has a long history. In 1953, polycarbonate was independently researched by Dr. H. Schnell of Bayer AG, Germany and D. W. Fox of the US Electric Power Company. It has been used in commercial applications since the late 1950s. Polycarbonate was originally used for electrical and electronic applications such as distribution and fuse boxes, displays and connectors, and glass for homes. glass and public buildings.
Polycarbonate's excellent combination of beneficial properties has made it the material of choice for many other applications.
In 1982, the first audio CD was introduced to the market, quickly replacing audio tapes. Within 10 years, optical communication technology included CD-ROM. Five years later, the first DVDs were released and were quickly followed by Bluray technology. All of these optical data storage systems depend on polycarbonate.
Since the mid-1980s, 18-liter water bottles made from polycarbonate and placed on water coolers have increasingly replaced heavy and fragile glass bottles.
These lightweight and shatterproof bottles can now be found in many public and office buildings.
Used in the US since the late 1980s, car headlights made from polycarbonate were authorized in Europe in 1992. Twenty years later, most European cars are equipped with polycarbonate headlights. polycarbonate.
Characteristic
Polycarbonate enables the production of high-performance engineering products in sophisticated forms and sizes. It improves quality of life and enhances safety and convenience for users and consumers around the world.
Its main benefits include:
• Durable
Polycarbonate plastic is a very durable material. This makes it the material of choice when the product life is long and efficient.
• Anti-breakage
Polycarbonate is virtually unbreakable. Through its high load capacity, it provides greater safety and comfort for applications where reliability and high performance are essential.
• Transparency
Polycarbonate is a transparent plastic material that has excellent visibility and transmits light better than other materials.
• Light-weight
Polycarbonate's light weight allows for architectural and design creativity. This leads to efficient use of resources and reduced financial and environmental costs of transportation.
• Heat resistance
Polycarbonate plastic provides excellent heat resistance, facilitating good cleaning at high temperatures.
• Creative potential
HThe performance of polycarbonate is continuously improving. Through technical and scientific innovation, new applications and product benefits are being offered, enabling market growth, providing consumers with additional services and benefits.
Application
These properties make polycarbonate suitable for many applications, including:
• Car
Polycarbonate mirror housing, tail lights, indicators, rear lights, fog lights and headlights all contribute to the vehicle's unique style.
• Pack
Polycarbonate bottles, containers and tableware can withstand extreme pressure during use and cleaning, including sterilization. They can be used to serve, freeze and reheat food in the microwave making them time-saving and energy-efficient. Waterproof and virtually unbreakable, polycarbonate is a safer alternative to glass.
• Household appliances and consumer goods
Polycarbonate's versatility in styling and coloring makes it perfect for use in electric kettles, refrigerators, food mixers, electric shavers and hair dryers, and meets all requirements. safety such as heat and insulation.
• Power electronics
Polycarbonate's lightweight and impact-resistant qualities make it perfect for cell phones, computers, fax machines and pagers while at the same time withstanding bumps, scratches and rough use. daily.
Production process
Polycarbonate is converted from fine powder or pellets into the desired shape for its intended application by heating the polycarbonate and pressing it under pressure into a mold or cavity to give it the desired shape depending on the application. use. This process is repeated continuously for a certain part, such as the cell phone housing. This part is usually sent to the manufacturer to assemble the final product.
There are two dominant processes in the production of products from polycarbonate:
• Extrusion:
The polymer is continuously forced through a pore, giving the molten polymer its final shape. After passing through the ice layer, the solvent dissolves quickly and solidifies, thus retaining a certain shape. This process makes it possible to produce long tubes, bars or plates.
• Molding:
The hot polymer is pressed into the mold.
The mold is then cooled, and the hot polymer solidifies over all mold properties. This process is used to produce final products, such as cases, plates, bottles, and many other applications.
High processability combined with excellent mechanical and physical properties make polycarbonate an excellent engineering plastic, and the material of choice for many high-quality, durable applications. This combination of features also allows designers extensive design freedom.
• Recycling and recovery
Application of PC plastic is 100% recyclable, either mechanically or as raw material, and energy from waste can be recovered in incinerators.
The most appropriate recovery option depends on many conditions, including local laws, plastic part design, access to sorting facilities, and regional logistics and recycling costs.
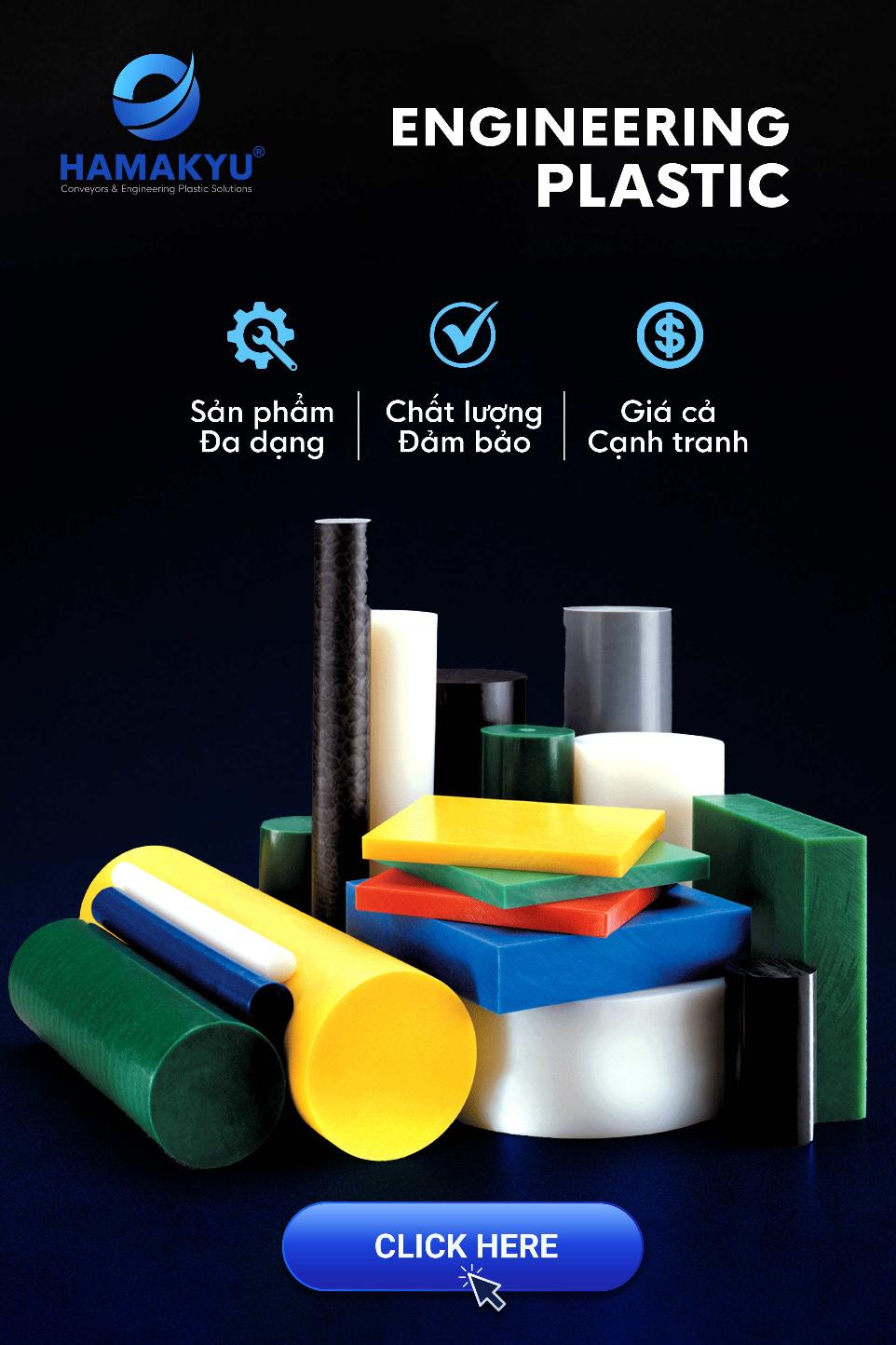