1. What is High Performance Plastics, How Are They Classified?
High-performance plastics are polymers with outstanding features and performance compared to standard plastics. The International Organization for Standardization (ISO) describes high performance plastics as "plastics that meet higher requirements than standard or engineering plastics because of their better thermal stability (usually above 150 °C), chemical stability (resistance against nearly all chemicals), mechanical properties (e.g., creep resistance), or electrical properties (e.g., dielectric strength)".
High-performance plastics must be categorized clearly since various sources may use different terms or criteria. However, Engineers did develop a standard classification system for high-performance polymers based on their thermal stability or heat resistance. This categorization system divides high performance polymers into three primary categories:
Standard High Performance Plastics:
These plastics' continuous service temperature (CST) is over 150 °C but less than 200 °C. Polyphenylene sulfide (PPS), polyetherimide (PEI), polyethersulfone (PES), polyetheretherketone (PEEK), polyimide (PI), and others are some examples of common high performance polymers.
Advanced High Performance Plastics:
CST for these polymers is more than 200 °C but less than 300 °C. Polybenzimidazole (PBI), polyetherketoneketone (PEKK), polyetherketone (PEK), polyaryletherketone (PAEK), and others are examples of advanced high performance polymers.
Extreme High Performance Plastics:
The CST of these polymers is more than 300 °C. Polytetrafluoroethylene (PTFE), fluorinated ethylene propylene (FEP), perfluoroalkoxy alkanes (PFA), and others are some examples of very high performance polymers.
Another way to classify high performance plastics is the basis of their chemical structure or composition. According to this classification scheme, there are four main groups of high performance plastics:
Fluoropolymers:
These are polymers with fluorine atoms built into their molecules. Fluoropolymers have great chemical resistance, thermal stability, electrical insulation, and minimal friction since fluorine is strongly electronegative. PTFE, FEP, PFA, and other fluoropolymers are among the examples.
Polyimides:
Imide groups (C=O-NH-C=O) are present in the molecular structure of these polymers. Imide groups have high stability and are radiation, chemical, and heat resistant. Polyimides include substances like PI, PBI, etc.
Polyaryletherketones:
The chemical structure of these polymers includes aryl ether groups (C-O-C) and ketone groups (C=O). Polyaryletherketones have great strength, stiffness, and thermal stability thanks to their aryl ether and ketone groups. PEEK, PEKK, PEK, PAEK, and other polyaryletherketones are a few examples.
Polyphenylene Sulfides:
The chemical structure of these polymers includes sulfide groups (S) and phenylene groups (C6H4). Thanks to phenylene and sulfide groups, Polyphenylene sulfides have great strength, stiffness, and chemical resistance. PPS, among others, are some examples of polyphenylene sulfides.
High-performance plastics are polymers with outstanding features and performance compared to standard plastics
2. What are Some Examples of High Performance Plastics and Their Properties?
Several varieties of high performance plastics are on the market, each with special qualities and attributes. Here are some examples of high performance plastics and their properties :
Name | CST (°C) | Density (g/cm³) | Tensile Strength (MPa) | Elongation at Break (%) | Flexural Modulus (GPa) | Impact Strength (kJ/m²) |
PPS | 200 | 1.35 | 75 | 2.5 | 3.8 | 15 |
PEI | 170 | 1.27 | 100 | 60 | 3.2 | 50 |
PES | 180 | 1.37 | 85 | 50 | 2.8 | 35 |
PEEK | 260 | 1.31 | 100 | 30 | 4.0 | 7 |
PI | 260 | 1.42 | 90 | 6.0 | 3.0 | 35 |
PBI | 400 | 1.31 | 110 | 2.5 | - | - |
PEKK | 260 | 1.32 | 105 | 50 | 4.1 |
3. What are Some Applications of High Performance Plastics in Various Industries?
Due to their improved characteristics and performance compared to ordinary plastics, high performance plastics have a broad variety of applications in several sectors. Here are some examples of applications of high performance plastics in different sectors:
3.1. Aerospace
High performance polymers are a popular option for aviation applications because of their superior strength-to-weight ratio, thermal stability, chemical resistance, and electrical insulation. High performance polymers use them in the following aircraft applications, for instance:
- Aircraft components
- Aircraft interiors
- Space applications
High performance polymers used in aircraft applications
3.2. Automotiveo
People often use high-performance polymers in automotive applications because of their utility, lightweight, toughness, and fuel efficiency. Several high performance plastics used in the automobile industry include:
- Engine and transmission parts
- Body and chassis parts
- Electrical and electronic parts
Several high performance plastics used in the automobile industry
3.3. Medical
Due to their biocompatibility, stabilizability, durability, and usefulness, high performance polymers are also often employed in medical applications. The following are some instances of high performance polymers used in medicine:
- Implants and prosthetics
- Surgical instruments and devices
- Diagnostic and therapeutic equipment
Implants and prosthetics
3.4. Electronics
Due to its electrical insulation, thermal stability, flame retardancy, and optical clarity, high performance polymers are often employed in electronics applications. High performance polymers use them in several electrical applications, for instance:
- Printed circuit boards
- Semiconductors and microchips
- Displays and screens
Printed circuit boards
4. Advantages of High Performance Plastics over Conventional Plastics
Due to their improved characteristics and performance, high performance plastics provide some benefits over traditional plastics. Some of the advantages of high performance plastics are:
Lightweight: High performance plastics are less dense than metals and ceramics, so they may lighten the load and cut the fuel requirements of machinery like cars and airplanes. For example, PEEK can replace aluminum and steel in aerospace applications, reducing the weight by up to 70%.
Durability: High performance plastics have a higher resistance to wear, fatigue, creep, and stress cracking than conventional plastics, which means they can last longer and require less maintenance. For example, PPS can replace brass and bronze in water valves, increasing the service life by up to 10 times.
Thermal stability: High performance plastics have a higher melting point and glass transition temperature than conventional plastics, which means they can withstand higher temperatures without degrading or losing their properties. For example, PBI can resist temperatures up to 400 °C without melting or burning.
Chemical resistance: High performance plastics have a higher resistance to acids, bases, solvents, oils, and gasses than conventional plastics, which can prevent corrosion and contamination. For example, PTFE can resist almost all chemicals without swelling or dissolving.
Electrical insulation: High performance plastics have a lower electrical conductivity and dielectric constant than metals and ceramics, which means they can prevent electrical shocks and interference. For example, PI can provide excellent electrical insulation and shield for wires and cables.
Optical clarity: High performance plastics have a higher transparency and refractive index than conventional plastics, which means they can provide better visibility and light transmission. For example, PES can provide high optical clarity and color fidelity for displays and screens.
PES can provide high optical clarity and color fidelity for displays and screens
5. Challenges and Limitations of High Performance Plastics
High performance plastics also have some challenges and limitations that have weighed them before use. Some of the challenges and limitations of high performance plastics are:
High cost: High performance plastics have a higher production cost than conventional plastics due to their complex synthesis, processing, and testing methods. They also have a higher market price due to their limited availability and demand. For example, PEEK can cost up to 100 times more than polyethylene.
Processing difficulties: High performance plastics have a higher processing temperature and pressure than conventional plastics due to their high melting point and viscosity. They also require special equipment, additives, and techniques for optimal properties and performance. For example, PTFE requires sintering at 370 °C under pressure to form solid shapes.
Environmental impact: High performance plastics have a higher environmental impact than conventional plastics due to their non-biodegradability and non-recyclability. They also generate more greenhouse gas emissions and toxic wastes during production and disposal. For example, PBI produces nitrogen oxides and hydrogen cyanide when burned.
PEEK can cost up to 100 times more than polyethylene
6. Conclusion
High-performance plastics are polymers with outstanding features and performance compared to standard plastics. They resist extreme conditions, including high heat, high pressure, corrosion, and abrasion. Additionally, they could provide improved biocompatibility, flame resistance, optical clarity, and lightweight functioning. High performance plastics are the best choice for difficult and crucial applications in the aerospace, automotive, medical, electronic, and other industries because of their properties.
High cost, complicated manufacture, negative environmental effects, and recycling concerns are just a few of the difficulties and limitations that high performance plastics must overcome. Thus, engineers and scientists must know the many high performance plastic kinds, uses, benefits, and obstacles to choose the ideal material for their unique demands.
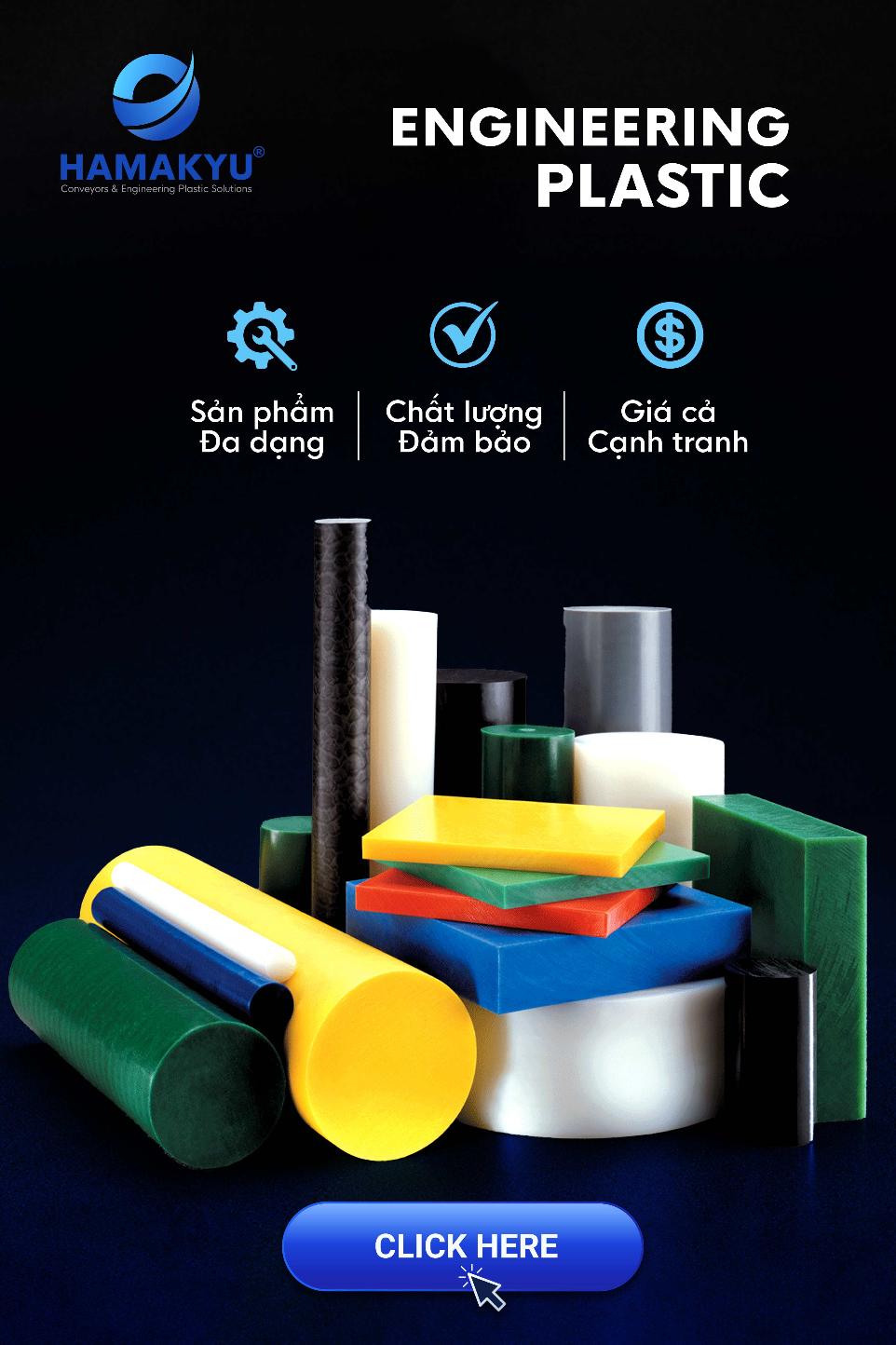