Guests or employees will slide on a 72 in (1.8 m vertical) buoy placed at each location of the swimming pool. Below the pool passengers pick up floats and transfer them to the inclined part of the conveyor belt and the belt carries the floats up to the tower. The inclined tape moves the floats into a fixed area or into a bin that will allow customers to pick them up and proceed to the starting position of the slide.
The conveyor rollers will be placed in a frame located at the two ends of the conveyor belt. The intermediate drums contribute to the inclined conveyor at the transition zones.
The take-up conveyor for the inclined surface (slope) will be powered by a gravity take-up located at the first support column. The wire brought up for supply will be through the stainless steel screw located on the tail section of that unit.
Hệ thống này sẽ có thể chuyền tải tối đa một chiếc cho mỗi 6 feet (2 mét) chiều dài băng tải nếu các bè được nạp liên tiếp. Bè sẽ đến điểm ở trên cùng khoảng 4 giây/cái.
Vật liệu xây dựng sẽ là thép không gỉ inox 304 ở tất cả mọi vị trí.
Tất cả các bề mặt khác được phủ hoặc mạ kẽm, cao su lưu hoá hoặc tráng men để ngăn chặn sự ăn mòn.
Tất cả các bộ phận không chuyển động (ví dụ: khung rào chắn) mà tiếp xúc với các phao phải phẳng và mịn để tránh thiệt hại cho chiếc phao.
Chú ý: Mục đích của hệ thống này là để truyền phao, không chở người lái, đủ bền để không bị hư hại.Nó không được thiết kế để di chuyển người hay thiết bị. Việc không tuân thủ này cảnh báo có thể dẫn đến chấn thương nghiêm trọng hoặc tử vong cá nhân.
Structure of float conveyor:
• Conveyor frame made from 304 stainless steel. The conveyor belt in horizontal position is connected and reinforced together, with legs supporting each section about 12 feet (3.8m).
• The conveyor belt is made of hot dipped galvanized steel welded structure, the conveyor frame is 304 stainless steel
The conveyor belt is to be reinforced mid-span with columns or concrete piers designed and supplied by other units.
• TEFC motor 1800 RPM with voltage and hertz (frequency unit) on request.
• Belt (chain) with a speed of 100 FPM.(feet/minute 30.48 meters/minute)
• Bearings use stainless steel. Use steel made from 304, 18-8, 410, 316.
• Flange made from stainless steel.
• All shafts made from 304 stainless steel with fitting upon request.
• The bearing is 6061 aluminum
• The frame can be easily and safely removed from stainless steel
The end of the conveyor belt has a stainless steel surround
Safety WARNING when using conveyor belts:
Never operate a conveyor without protection installed.
• 2.375" (6.01 cm) Ø PVC Is the roller diameter and is attached to a steel frame with
Bearing made from stainless steel.
• The belt is made of PVC type FS x FS with stainless steel SJ 180 clamp clamped
• Stainless and hot galvanized surfaces shall not be painted.
• Carbon steel housing on electric motor and gear shaft will be enameled. The case is made from steel
casting.
• All screws are stainless steel or hot-dip galvanized.
• The entire length of stainless steel guide is approximately 7" (18 cm) above the base on either side of the tape.
Float conveyor control system:
The conveyor system is provided with a control panel consisting of motors, relays, timers, optical sensors and terminal blocks.
General specifications are as follows:
• NEMA 4X non-metallic electronic enclosure.
• VFD starter motor..
• Two control points at both ends of the chain. The control box has 2 buttons "On" and stop. Voltage
Control center controller is 24V. installed in a watertight box installed near the top and bottom of the
Conveyor system:
•Control panel for cross-lock interlock type safety disconnection.
• The control circuits are designed to be completely automatic
• power and electrical services may be provided by other means.
Safety in conveyor transport:
Electrical control panels and remote controls must be installed in locations where containment is possible. Do not expose to the activities of personnel or other unrelated persons standing, or being directly exposed to water.
Floating conveyor system to the top:
Slide on a 72 in buoy (1.8 m vertical).
- Semi-submersible feeding structure, can be submerged in water 29 feet (nearly 9m), shaft can be tilted 214 feet long (nearly 66m) with a 9 degree inclination.
- All steel frame requirements are 304 stainless steel and are the same as those of Tower A
Conveyor requirements:
- 2.375" (6.01 cm) Ø PVC Is the roller diameter and is attached to a steel frame with
- Bearing made from stainless steel.
- Belt made from SBR plastic with SJ 125 clamp made from stainless steel.
- Every 48 feet (14.5 m) along the length will have supporting columns.
- There is a wind shield covering the outside of the 48 feed belt.
- ELECTRICAL CONTROL in conveyor system.
The conveyor system is provided with a control panel consisting of motors, relays,
timers (counters, timers), optical sensors and terminal blocks.
- General technical specifications are as follows:
• NEMA 4X non-metallic electronic enclosure.
• VFD starter motor..
• Two control points at both ends of the chain. The control box has 2 buttons "On" and stop. Electricity
Control center control voltage is 24V. installed in a watertight box installed near the top
and the bottom of the conveyor system.
• Control panel for cross-lock interlock type safety disconnection.
• The control circuits are designed to be completely automatic
• power and electrical services may be provided by other means.
- Eye image control system will automatically start and stop the conveyor belt
This feature eliminates attendants to operate conveyor controls.
- For every 12 feet (3m6) of transport, 1 cannon will be issued and after 10 seconds there will be 1 float to the top.
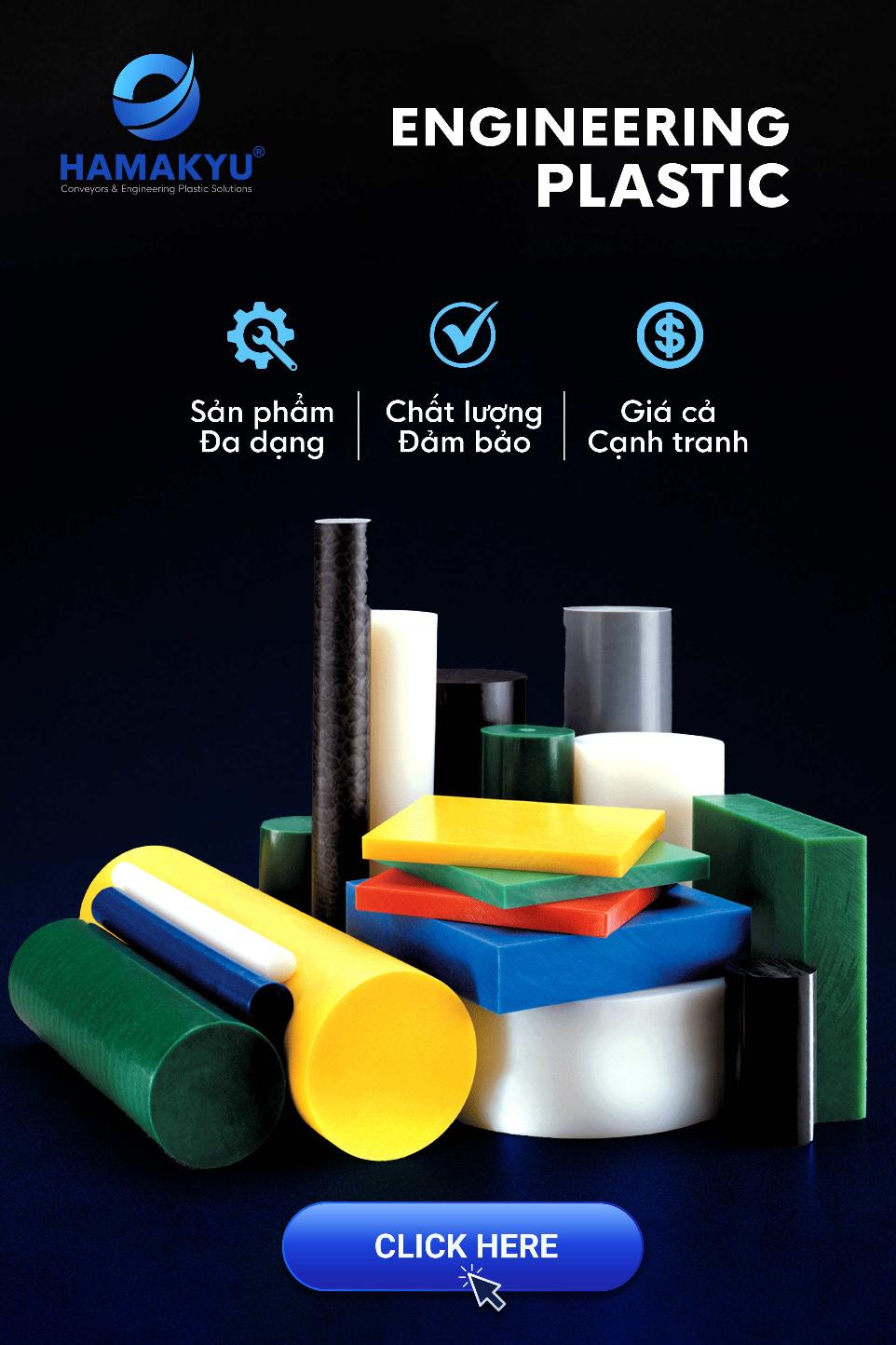